1.3 試驗(yàn)方法與分析方法
萃取脫芳烴:取一定配比的原料油與A劑混合,放置在恒溫水浴中,達(dá)到萃取溫度后震蕩一定時(shí)間,將混合液倒入置于恒溫水浴的分液漏斗中,靜置分相,下相為芳烴富液(A劑+芳烴)、上相為脫芳烴油。B劑與脫芳烴油完全不互溶,脫芳烴油中夾帶的殘余A劑可采用B劑洗滌回收。
芳烴回收:采用B劑萃取芳烴富液(A劑+芳烴)中的A劑,多環(huán)芳烴在B劑中完全不溶解從而被分離出來,得到混合芳烴產(chǎn)品。按一定的比例將B劑和芳烴富液(A劑+芳烴)混合,放置在恒溫水浴中,達(dá)到萃取溫度后震蕩一定時(shí)間,將混合液倒入置于恒溫水浴的分液漏斗中,靜置分相,下相為(A劑+B劑)、上相為混合芳烴產(chǎn)品,然后測(cè)定其質(zhì)量并采用色質(zhì)聯(lián)用儀分析其組成。
反萃?。翰捎肅劑萃取液相(A劑+B劑)中的A劑,B劑在C劑中不溶解從而被分離出來,得到再生B劑。按一定的比例將C劑和液相(A劑+B劑)混合,置于恒溫水浴中,達(dá)到萃取溫度后震蕩一定時(shí)間,將混合液倒入分液漏斗中恒溫靜置分相,下相為(A劑+C劑)、上相為再生B劑。
溶劑再生:取一定量的液相(A劑+C劑)置于圓底燒瓶中,進(jìn)行減壓蒸餾,回收C劑,同時(shí)得到再生芳烴萃取溶劑A劑。
分析方法:采用美國安捷倫公司生產(chǎn)的7890A/5975C-GC/MSD型色質(zhì)聯(lián)用儀測(cè)定原料油及芳烴的組成,定量分析采用面積歸一法,分析精度為3 μg/g。
2 結(jié)果與討論
2.1 脫芳烴操作條件的優(yōu)化
2.1.1 萃取溫度在A劑催化柴油體積比為1.5、萃取時(shí)間為5 min、相分離時(shí)間為5 min的條件下,萃取溫度(相分離溫度)對(duì)催化柴油脫芳烴效果的影響見圖1。
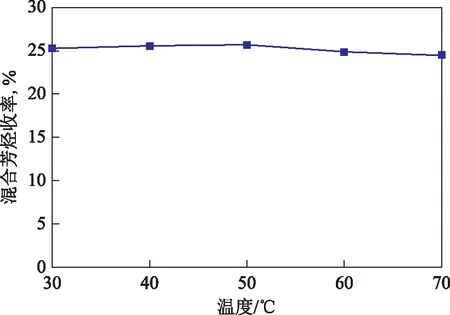
圖1 萃取溫度對(duì)脫芳烴效果的影響
由圖1可見,隨著溫度的升高,混合芳烴收率先逐漸增加后下降,當(dāng)溫度為50 ℃時(shí)最高,達(dá)到25.71%。理論上較高的溫度有利于分子的熱運(yùn)動(dòng)并促進(jìn)分子之間的相互作用,引起較高的溶劑溶解能力,適當(dāng)提高溫度有利于萃取體系的相分離,但較高的溫度會(huì)導(dǎo)致芳烴在油劑兩相中重新分配,改變相平衡狀態(tài),導(dǎo)致脫芳烴率降低。因此,選擇最佳萃取溫度為50 ℃。
2.1.2 萃取時(shí)間在A劑催化柴油體積比為1.5、萃取溫度為50 ℃、相分離時(shí)間為5 min的條件下,萃取時(shí)間對(duì)脫芳烴效果的影響見圖2。

圖2 萃取時(shí)間對(duì)脫芳烴效果的影響
由圖2可見,隨著萃取時(shí)間的增加,混合芳烴收率先逐漸增加后趨于平穩(wěn),萃取時(shí)間超過5 min時(shí),混合芳烴收率為26.10%,液液兩相達(dá)到平衡,繼續(xù)增加萃取時(shí)間,混合芳烴收率幾乎不變。因此,選擇最佳萃取時(shí)間為5 min。
2.1.3 相分離時(shí)間在A劑催化柴油體積比為1.5、萃取溫度為50 ℃、萃取時(shí)間為5 min的條件下,相分離時(shí)間對(duì)脫芳烴效果的影響見圖3。
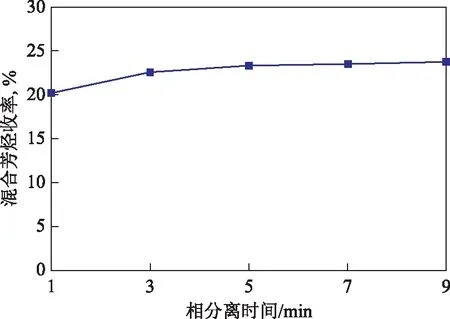
圖3 相分離時(shí)間對(duì)脫芳烴效果的影響
由圖3可見,隨著相分離時(shí)間的增加,混合芳烴收率先增加后趨于平穩(wěn),當(dāng)相分離時(shí)間超過5 min時(shí),液液兩相達(dá)到平衡,混合芳烴收率幾乎不變,為27.64%。因此,選擇最佳相分離時(shí)間為5 min。
2.1.4 劑油比在萃取溫度為50 ℃、萃取時(shí)間為5 min、相分離時(shí)間為10 min的條件下,劑油比對(duì)脫芳烴效果的影響見圖4。

圖4 劑油比對(duì)脫芳烴效果的影響
由圖4可見:隨著劑油比增加,混合芳烴收率逐漸增加;當(dāng)A劑催化柴油體積比為1時(shí),混合芳烴收率為26.30%,其芳烴質(zhì)量分?jǐn)?shù)高達(dá)93.84%;當(dāng)A劑催化柴油體積比為1.5時(shí),混合芳烴收率提高到29.29%,其芳烴質(zhì)量分?jǐn)?shù)為93.71%;當(dāng)A劑催化柴油體積比大于1.5時(shí),混合芳烴收率繼續(xù)提高,但芳烴含量則減小。原因是隨著劑油比增加,萃取劑對(duì)芳烴的選擇性降低,使得柴油中理想組分被萃取出來,導(dǎo)致混合芳烴產(chǎn)品中的芳烴含量下降。因此,選擇最佳A劑催化柴油體積比為1.5。
2.2 芳烴回收單元操作條件的優(yōu)化
2.2.1 萃取溫度在B劑(A劑+芳烴)體積比為0.2、萃取時(shí)間為4 min、相分離時(shí)間為3 min的條件下,萃取溫度對(duì)芳烴回收效果的影響見圖5。
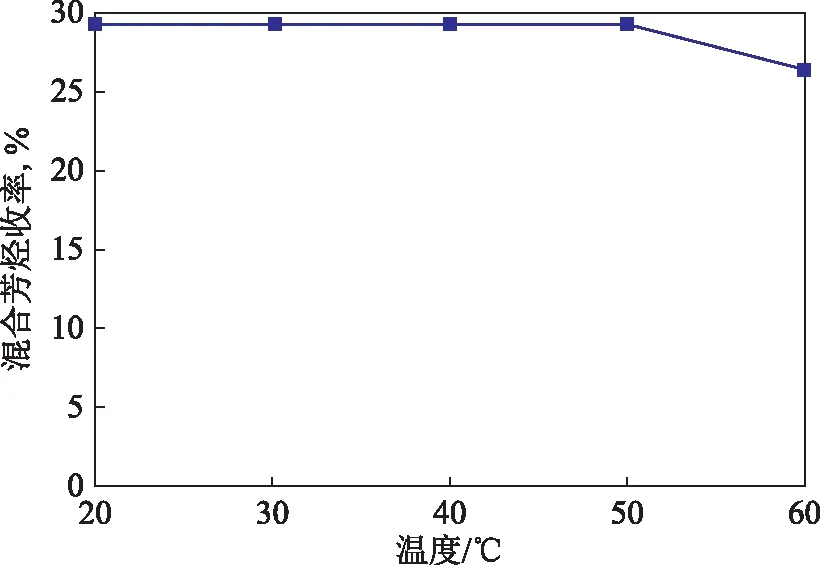
圖5 萃取溫度對(duì)芳烴回收效果的影響
由圖5可見:當(dāng)萃取溫度低于50 ℃時(shí),混合芳烴收率隨著萃取溫度升高而不變;當(dāng)萃取溫度超過50 ℃時(shí),混合芳烴收率反而減小。由于萃取溫度較低時(shí),分子間的運(yùn)動(dòng)較弱,導(dǎo)致相分離時(shí)間變長(zhǎng);而溫度過高,混合芳烴在B劑中的溶解度增大,導(dǎo)致芳烴收率減少。因此,選擇最佳萃取溫度為50 ℃。
2.2.2 萃取時(shí)間在B劑(A劑+芳烴)體積比為0.2、萃取溫度為50 ℃、相分離時(shí)間為3 min的條件下,萃取時(shí)間對(duì)芳烴回收效果的影響見圖6。
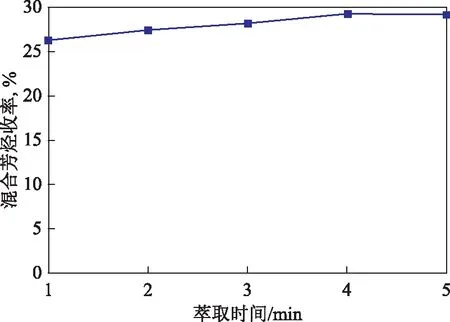
圖6 萃取時(shí)間對(duì)芳烴回收效果的影響
由圖6可見,當(dāng)萃取時(shí)間小于4 min時(shí),混合芳烴收率隨著萃取時(shí)間的延長(zhǎng)而增加,當(dāng)萃取時(shí)間大于4 min時(shí),混合芳烴收率不再變化,此時(shí)液液兩相達(dá)到平衡。因此,選擇最佳萃取時(shí)間為4 min。
2.2.3 相分離時(shí)間在B劑(A劑+芳烴)體積比為0.2、萃取溫度為50 ℃、萃取時(shí)間為4 min的條件下,相分離時(shí)間對(duì)芳烴回收效果的影響見圖7。

圖7 相分離時(shí)間對(duì)芳烴回收效果的影響
由圖7可見:當(dāng)相分離時(shí)間小于3 min時(shí),混合芳烴收率隨著相分離時(shí)間的延長(zhǎng)而增大;當(dāng)相分離時(shí)間大于3 min時(shí),混合芳烴收率則趨于平穩(wěn)。這是因?yàn)殡S著相分離時(shí)間的延長(zhǎng),液液兩相達(dá)到平衡。因此,選擇最佳相分離時(shí)間為3 min。
2.2.4 劑液比在萃取溫度為50 ℃、萃取時(shí)間為4 min、相分離時(shí)間為3 min的條件下,劑液比對(duì)芳烴回收效果的影響見圖8。

圖8 劑液比對(duì)芳烴回收效果的影響
在優(yōu)化的操作條件下對(duì)催化柴油萃取脫芳烴,檢測(cè)脫芳烴油和混合芳烴產(chǎn)品的組成和殘余溶劑含量,結(jié)果見表1。
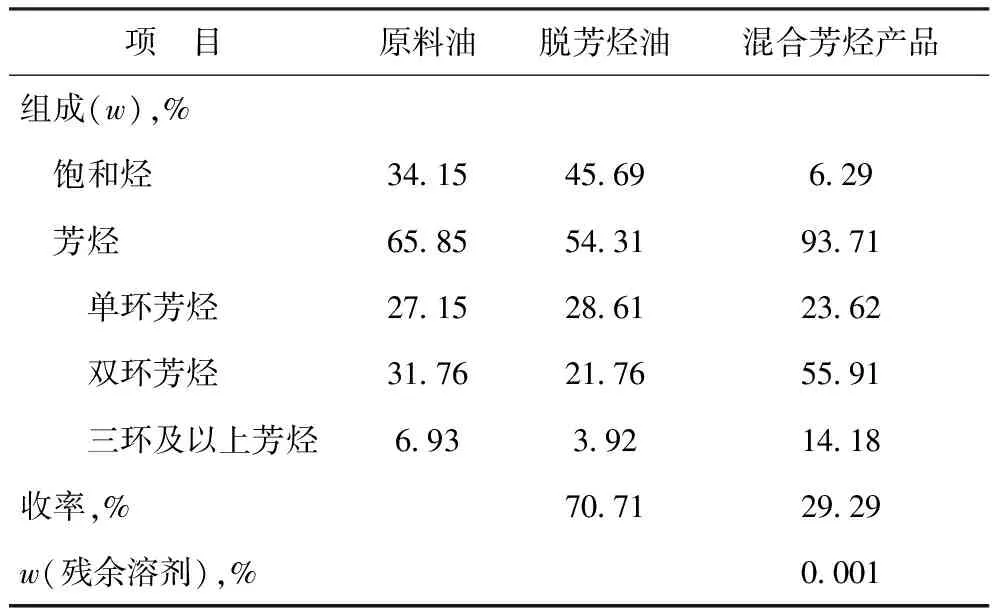
表1 催化柴油萃取前后組成
由表1可見:萃取后脫芳烴油中飽和烴含量增大、芳烴含量減少;混合芳烴產(chǎn)品收率為29.29%,其芳烴質(zhì)量分?jǐn)?shù)為93.71%;脫芳烴油中無殘余溶劑,混合芳烴產(chǎn)品中殘余溶劑的質(zhì)量分?jǐn)?shù)為0.001%。
2.3 反萃取操作條件的優(yōu)化
2.3.1 反萃取溫度在C劑(A劑+B劑)體積比為0.2、反萃取時(shí)間為3 min、相分離時(shí)間為3 min的條件下,反萃取溫度(相分離溫度)對(duì)溶劑B劑回收率的影響見圖9。

圖9 反萃取溫度對(duì)B劑回收率的影響
由圖9可見:當(dāng)反萃取溫度低于40 ℃時(shí),B劑回收率隨著溫度的升高而增加;當(dāng)溫度高于40 ℃時(shí),B劑回收率隨著溫度的升高而減少。這是因?yàn)榉摧腿囟容^低時(shí),不利于分子之間的熱運(yùn)動(dòng)且相分離時(shí)間較長(zhǎng);當(dāng)反萃取溫度過高時(shí),又導(dǎo)致A劑和B劑互溶,分離回收B劑困難。當(dāng)溫度為40 ℃時(shí),B劑回收率為100%。因此,選擇最佳反萃取溫度為40 ℃。
2.3.2 反萃取時(shí)間在C劑(A劑+B劑)體積比為0.2、反萃取溫度為40 ℃、相分離時(shí)間為3 min的條件下,反萃取時(shí)間對(duì)B劑回收率的影響見圖10。
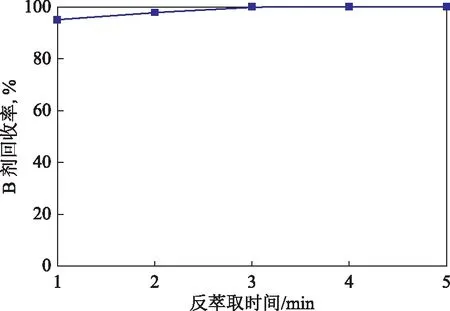
圖10 反萃取時(shí)間對(duì)B劑回收率的影響
由圖10可見:當(dāng)反萃取時(shí)間小于3 min時(shí),B劑回收率隨萃取時(shí)間的增加而增大;當(dāng)萃取時(shí)間大于3 min時(shí),B劑回收率趨于平穩(wěn)(100%)。因此,選擇最佳反萃取時(shí)間為3 min。
2.3.3 相分離時(shí)間在C劑(A劑+B劑)體積比為0.2、反萃取溫度為40 ℃、反萃取時(shí)間為3 min的條件下,相分離時(shí)間對(duì)B劑回收率的影響見圖11。

圖11 相分離時(shí)間對(duì)B劑回收率的影響
由圖11可見:當(dāng)相分離時(shí)間小于3 min時(shí),B劑回收率隨著相分離時(shí)間的增加而增大;當(dāng)相分離時(shí)間大于3 min時(shí),B劑回收率趨于穩(wěn)定(100%)。由于相分離時(shí)間大于3 min時(shí)液液兩相達(dá)到了平衡,延長(zhǎng)相分離時(shí)間對(duì)B劑回收率影響不大。因此,選擇最佳相分離時(shí)間為3 min。
2.3.4 劑液比在反萃取溫度為40 ℃、反萃取時(shí)間為3 min、相分離時(shí)間為3 min的條件下,劑液比對(duì)B劑回收率的影響見圖12。

圖12 劑液比對(duì)B劑回收率的影響
2.4 溶劑再生
環(huán)丁砜(A劑)和C劑回收的主要原理是利用二者之間的沸點(diǎn)不同,采用減壓蒸餾(溫度78 ℃、壓力0.04~0.05 MPa)回收C劑(塔頂)和環(huán)丁砜(塔釜),將回收的再生溶劑進(jìn)行循環(huán)使用。再生溶劑與新鮮溶劑的萃取脫芳烴效果對(duì)比見表2。由表2可知,新鮮溶劑與再生溶劑萃取效果相當(dāng)。

表2 再生溶劑與新鮮溶劑的萃取脫芳烴效果比較
3 工藝流程
催化柴油常壓低溫萃取脫芳烴的原則工藝流程如圖13所示。

圖13 催化柴油脫芳烴的原則工藝流程
催化柴油脫除多環(huán)芳烴工藝主要由脫芳烴系統(tǒng)、芳烴回收系統(tǒng)和溶劑再生系統(tǒng)組成,工藝流程簡(jiǎn)單;與傳統(tǒng)的芳烴抽提裝置相比,本萃取工藝采用反萃取溶劑對(duì)富溶劑進(jìn)行反萃取,在40~80 ℃、常壓條件下萃取,溶劑在78 ℃、0.04~0.05 MPa條件下再生,只需要100~120 ℃(0.1~0.2 MPa)蒸汽,能耗低,解決了現(xiàn)有工藝存在的高溫反復(fù)作用導(dǎo)致溶劑性能惡化的問題。與現(xiàn)有工藝采用的1.0~3.5 MPa(180~240 ℃)高溫蒸汽比較,0.1~0.2 MPa(100~120 ℃)蒸汽價(jià)格不到前者的一半,可以采用煉油廠的低溫位熱源甚至廢熱源。經(jīng)過測(cè)算,以300 kt/a催化裂化柴油萃取脫芳烴裝置規(guī)模為例(目前只能與同規(guī)模的重整汽油芳烴抽提裝置比較),可節(jié)約3.5 MPa蒸汽49.2 kt/a,節(jié)約操作費(fèi)用1 214萬元/a。
此外,脫除柴油中的多環(huán)芳烴后,在降低柴油產(chǎn)量的同時(shí)可大幅度提高柴油質(zhì)量,獲得的多環(huán)芳烴可作為精細(xì)化工原料,用于合成多環(huán)芳烴樹脂、固體磺酸催化劑、離子交換樹脂、高比表面活性炭、碳纖維和納米碳材料等。進(jìn)一步分析表明,該工藝還可用于低芳烴石腦油、重整汽油、焦化柴油等原料的脫芳烴,以及潤(rùn)滑油糠醛精制工藝。
4 結(jié) 論
(1)在評(píng)選出的最佳催化裂化柴油萃取脫芳烴條件和芳烴回收條件下,多環(huán)芳烴產(chǎn)品收率為29.29%,其芳烴質(zhì)量分?jǐn)?shù)為93.71%。
(2)在評(píng)選出的最佳反萃取條件以及減壓蒸餾(溫度78 ℃、壓力0.04~0.05 MPa)條件下對(duì)溶劑進(jìn)行再生回收,再生溶劑用于脫芳烴,混合芳烴收率為29.47%,芳烴質(zhì)量分?jǐn)?shù)為93.69%,其脫芳烴效果與新鮮溶劑相當(dāng)。
(3)采用0.1~0.2 MPa低溫蒸汽替代1.0~3.5 MPa高溫蒸汽進(jìn)行溶劑再生,大大降低過程能耗,萃取劑循環(huán)使用,實(shí)現(xiàn)了零排放,解決了現(xiàn)有工藝存在的高溫反復(fù)作用導(dǎo)致溶劑性能惡化的問題。
(4)提出了催化裂化柴油液-液萃取脫芳烴的原則工藝流程,該萃取工藝采用液-液萃取和反萃取,取代了傳統(tǒng)的芳烴抽提蒸餾,并采用低溫(<100 ℃)減壓蒸餾再生,該技術(shù)路線為柴油萃取脫芳烴的工業(yè)應(yīng)用提供了新思路。