
表2 9個最嚴(yán)重金屬損失異常點的腐蝕損傷類別Tab. 2 Category of corrosion damage for 9 most serious metal loss anomalies
2.2.2 管道點蝕速度和穿孔年限估算
根據(jù)SYT 0087-1995《鋼質(zhì)管道及儲罐腐蝕與防護(hù)調(diào)查方法標(biāo)準(zhǔn)》,對9個最嚴(yán)重金屬損失點的點蝕速度和穿孔年限進(jìn)行評價,結(jié)果見表3。
由表3可見:9個最嚴(yán)重的金屬損失異常點中,壁厚損失為25%~42%的5個最嚴(yán)重金屬損失異常點的點蝕速率為0.611~2.438 mm/a,屬于“重”度點蝕,其點蝕穿孔年限為3~5 a;壁厚損失為23%~21%的4個嚴(yán)重金屬損失異常點的點蝕速率為0.305~0.611 mm/a,屬于“中”度點蝕,其點蝕穿孔年限為5~10 a。
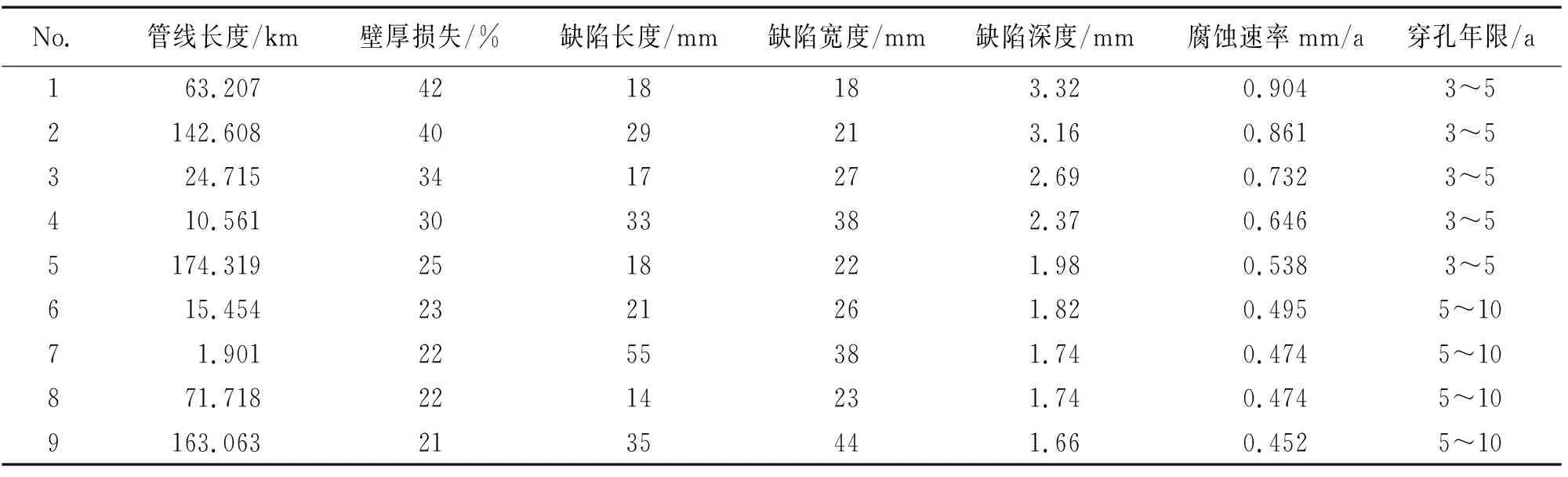
表3 9個最嚴(yán)重金屬損失異常點的點蝕速度和穿孔年限估算結(jié)果Tab. 3 Estimation results of corrosion velocity and perforation period for 9 most serious metal loss anomalies
3 最嚴(yán)重金屬損失異常點的壓力分析計算
3.1 最小失效壓力
實際工作時的管道處于復(fù)雜受力狀態(tài),其破裂機(jī)理也十分復(fù)雜。管道失效壓力是描述在極限受力狀態(tài)或極限應(yīng)變狀態(tài)下,管道因為壓力過大而喪失正常工作能力,發(fā)生強(qiáng)度失效(如破裂)、剛度失效(如彈性變形)、穩(wěn)定失效(如穿孔或泄漏)等現(xiàn)象的強(qiáng)度理論或失效判據(jù)。在這些判據(jù)里,規(guī)定的表征達(dá)到管道失效時的壓力,就稱為管道失效壓力。
按照SYT 0087.2-2012《埋地鋼質(zhì)管道內(nèi)腐蝕直接評價》,σs取448 MPa,t取7.90 mm,D取508 mm,按照腐蝕深度d對該原油管道內(nèi)檢測數(shù)據(jù)中9個最嚴(yán)重金屬損失異常點的最小失效壓力Pd進(jìn)行計算,結(jié)果見表4。
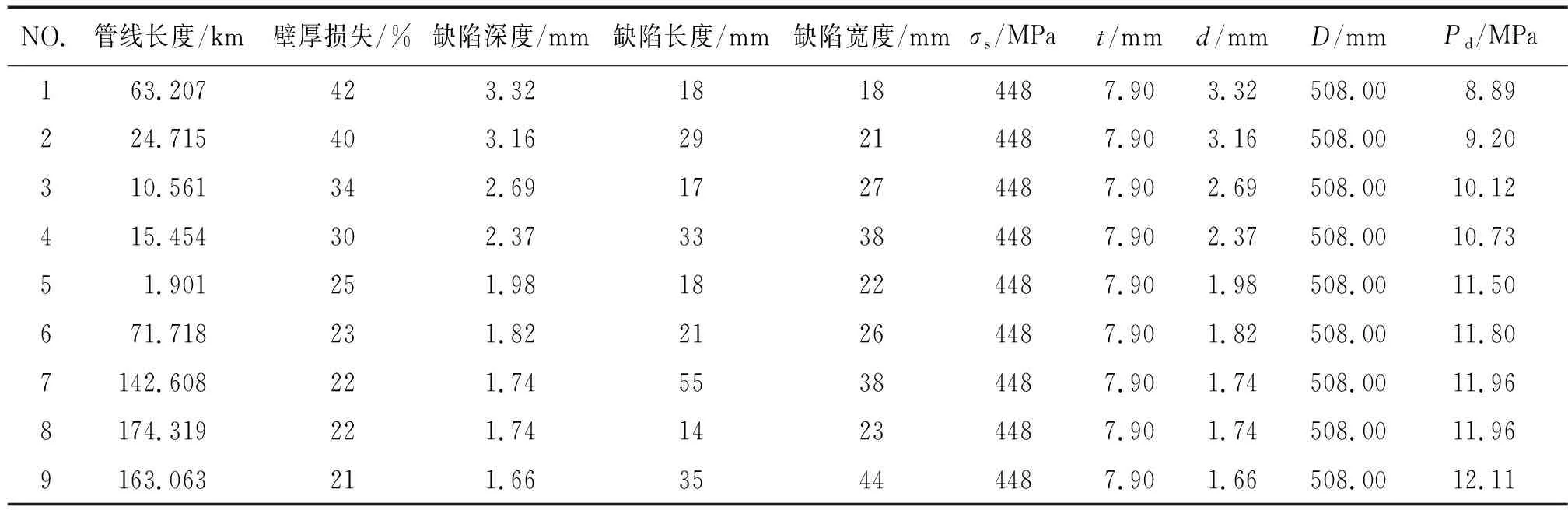
表4 9個最嚴(yán)重金屬損失異常點的最小失效壓力Tab. 4 Minimum failure pressure for 9 most serious metal loss anomalies
3.2 最大安全工作壓力
按照SYT 6151-2009《鋼質(zhì)管道管體腐蝕損傷評價方法》第A.3條中的計算方法,MAOP(最大允許工作壓力)取值9.80 MPa,t取值7.90 mm,按照腐蝕深度d對該原油管道內(nèi)檢測數(shù)據(jù)中9個最嚴(yán)重金屬損失點所能承受的最大安全工作壓力(Psw)進(jìn)行計算,結(jié)果見表5。
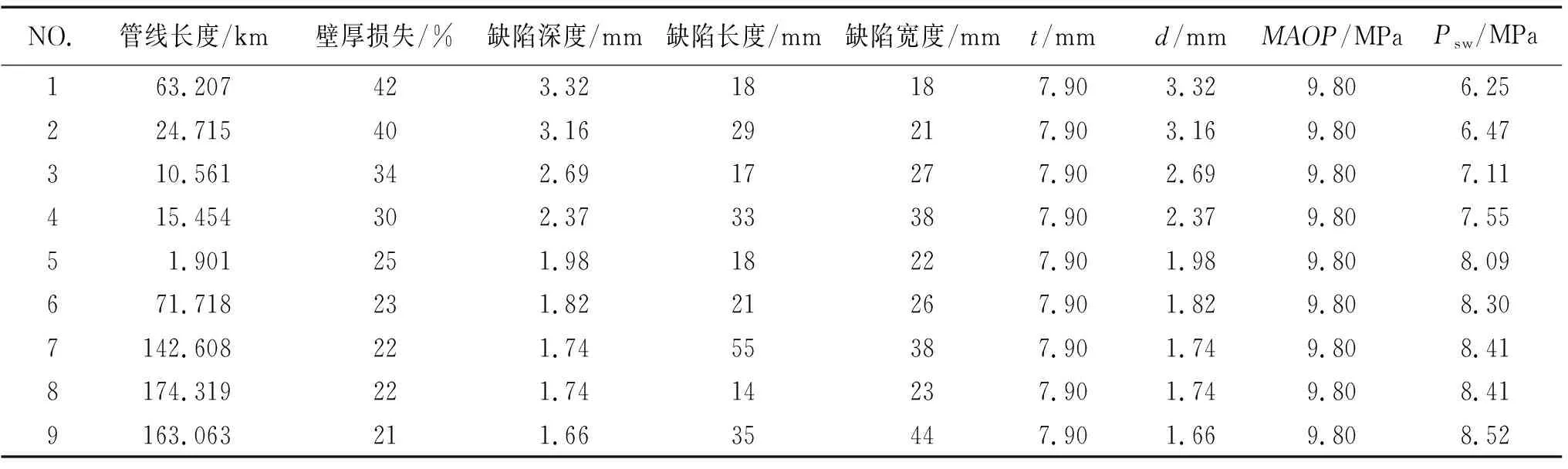
表5 9個最嚴(yán)重金屬損失異常點的最大安全工作壓力計算表Tab. 5 Maximum safety work pressure calculating table for 9 most serious metal loss anomalies
3.3 最嚴(yán)重金屬損失點的模擬運行壓力推算
根據(jù)達(dá)西公式和管道全線沿程的摩阻計算管道水力摩阻系數(shù)λ,見式(1)和(2)。
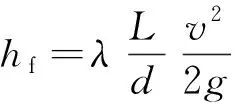
(1)
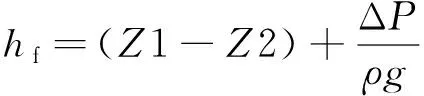
(2)
式中:Z1-Z2為管道沿線起點和終點高程差(本工作中取196 480 m),ΔP為管道起終點間壓降(本工作中取3.35 MPa),ρ為原油密度(本工作中取 875.5 kg/m3),g為重力加速度,L為起點和終點距離(本工作中取-63 m),v為管道流速(本工作中取 493 m3/h),d為管道內(nèi)徑(本工作中取 0.492 2 m),λ為水力摩阻系數(shù)。結(jié)合目前管道密閉輸油工況,忽略站場之間的摩阻,計算得到水力摩阻系數(shù)為0.030 999 349。
根據(jù)雷諾數(shù)Re,目前管道水力工況為水力光滑區(qū),通過迭代,當(dāng)管道流量為662 m3/h(500萬 t/a,10萬桶/d)時,管道水力工況仍為水力光滑區(qū)。
通過水力摩阻系數(shù)λ,首先設(shè)定末站進(jìn)站壓力為0.5 MPa,然后根據(jù)經(jīng)驗公式計算得出異常點至末站壓降,最后反推計算出500萬t/a工況下9個最嚴(yán)重金屬損失異常的模擬運行壓力,見表6。
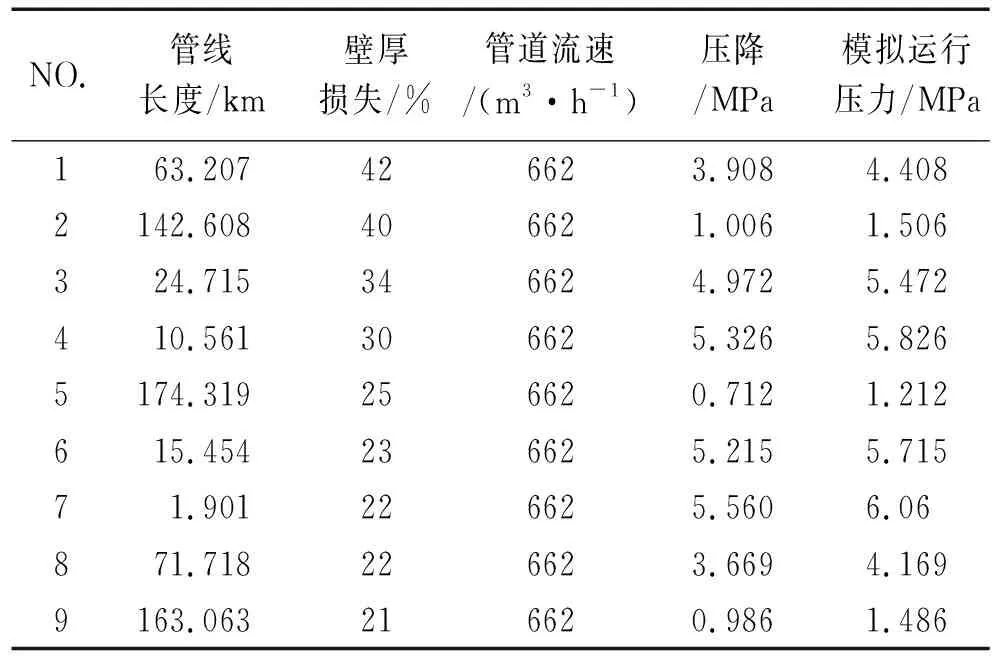
表6 9個最嚴(yán)重金屬損失異常點的模擬運行壓力Tab. 6 Simulated operating pressure calculating table for 9 most serious metal loss anomalies
3.4 最嚴(yán)重金屬損失異常點的壓力
管道失效壓力描述的是管道發(fā)生失效現(xiàn)象的極限值,故管道失效壓力大于管道設(shè)計壓力屬于正常情況。選取9個最嚴(yán)重金屬損失點所能承受的最小失效壓力,作為管道失效壓力參考數(shù)據(jù)。
現(xiàn)階段實際運行工況下的管道流量為350萬t/a,參考該原油管道實際運行壓力,計算出的9個最嚴(yán)重金屬損失點所能承受的最大安全工作壓力,可以作為該原油管道日常運行過程中各金屬損失點的壓力監(jiān)測和控制上限值。
按照首站至末站方向進(jìn)行距離排序,將該原油管道內(nèi)檢測數(shù)據(jù)中9個最嚴(yán)重金屬損失點的高程、模擬運行壓力、最大安全工作壓力及兩個壓力差值列于表7。
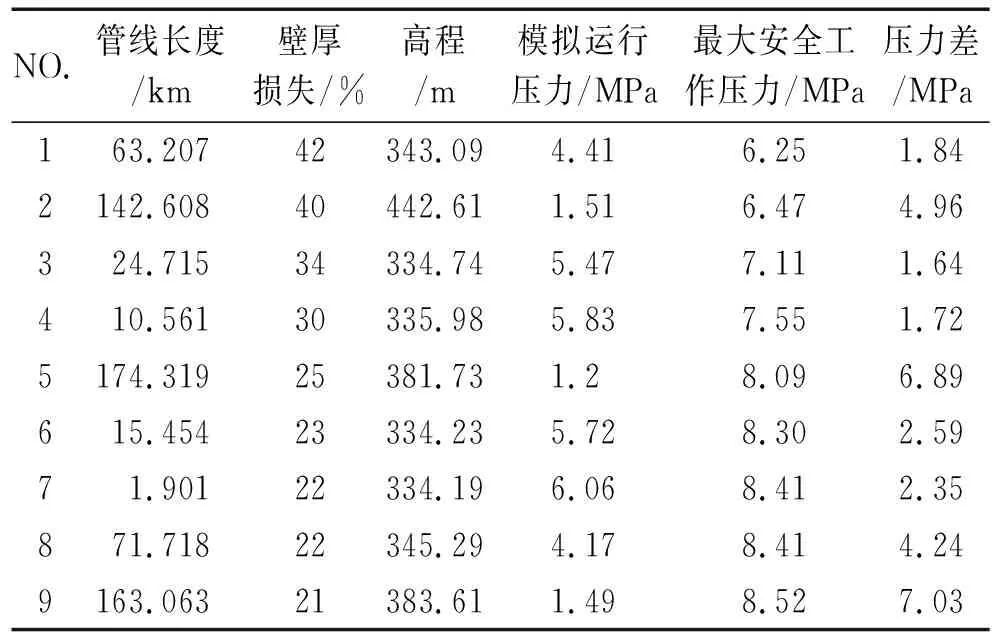
表7 9個最嚴(yán)重金屬損失異常點的壓力差值Tab. 7 Pressure difference for 9 most serious metal loss anomalies
計算得出,500萬t/a輸油工況下,該原油管道內(nèi)檢測數(shù)據(jù)中9個最嚴(yán)重金屬損失點的最大模擬運行壓力為6.06 MPa。由于142.608 km金屬異常點處于管段翻越段,因此壓力會出現(xiàn)升高,屬于正常情況。5個重度金屬損失點中,檢測里程為142.608 km和174.319 km的2個異常點處于整個管道的后半段;檢測里程為10.561,24.715,63.207 km的3個異常點處于整個管道的前半段。在500萬t/a輸油工況下,管道后半段2個異常點的模擬運行壓力遠(yuǎn)低于估算的最大安全工作壓力;管道前半段3個異常點的模擬運行壓力接近估算的最大安全工作壓力,其壓力差值小于2 MPa。
4 漏磁內(nèi)檢測準(zhǔn)確度的驗證
4.1 開挖驗證點的選取
為驗證該原油管道本次內(nèi)檢測結(jié)果的準(zhǔn)確程度和檢測的置信水平,并對比開挖驗證實際結(jié)果與漏磁內(nèi)檢測實際結(jié)果的符合度。綜合考慮檢測公司提供的內(nèi)檢測最終報告數(shù)據(jù)、9個最嚴(yán)重金屬損失異常點的腐蝕評價和壓力分析等相關(guān)內(nèi)容,最終確定6個最嚴(yán)重金屬損失點、1個最嚴(yán)重凹型形變和1個腐蝕團(tuán)簇共計8個內(nèi)檢測異常點作為缺陷點進(jìn)行開挖驗證,選取的8個缺陷異常點的詳細(xì)信息見表8。
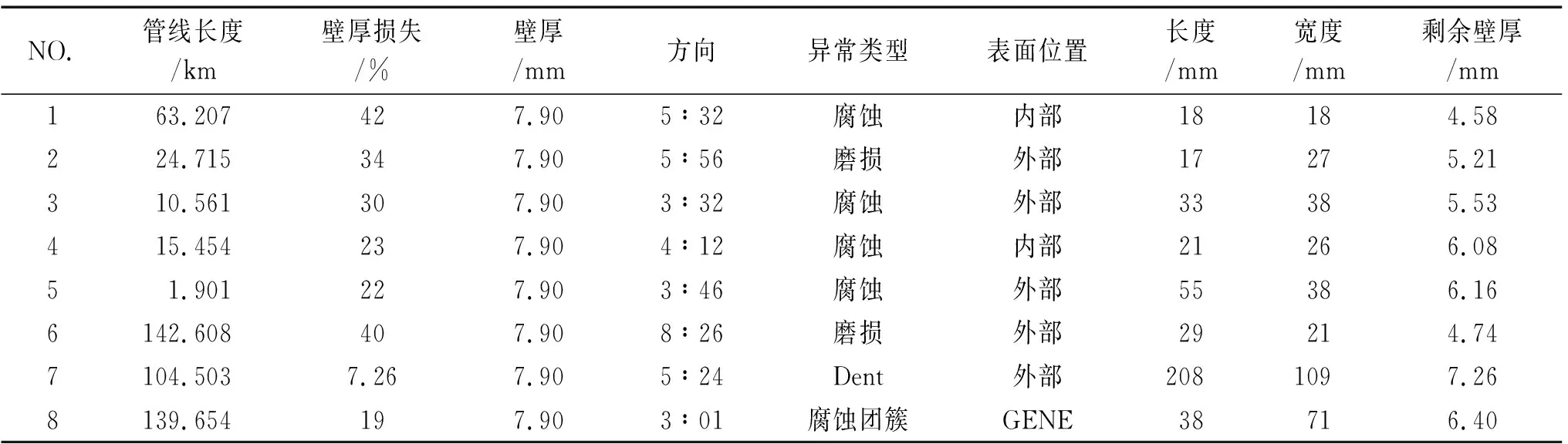
表8 8個實施開挖驗證的異常點的詳細(xì)信息Tab. 8 Statistical table of 8 anomalies performed excavation verification
4.2 開挖驗證點的定位
本次原油管道漏磁內(nèi)檢測作業(yè)中,對管道腐蝕缺陷定位所使用的是里程輪法和地面標(biāo)記系統(tǒng)。漏磁內(nèi)檢測使用反滲透高分辨率機(jī)械檢測球,檢測球的電子系統(tǒng)將發(fā)球筒后第一個閥門的中心距離作為主要參考,并設(shè)置為0.000 m。當(dāng)檢測球在原油管道中行進(jìn)時,由檢測球自帶的里程輪對管道檢測里程、上下游焊縫間距和缺陷異常點位置等信息進(jìn)行標(biāo)定和記錄。
地面標(biāo)記系統(tǒng)是管道檢測球的配套設(shè)備之一,也是檢測器提高定位精度的重要輔助設(shè)備,它能夠檢測并記錄檢測球通過設(shè)標(biāo)參考點的時間。檢測前,采用基準(zhǔn)時鐘設(shè)備對檢測球的電子系統(tǒng)和地面標(biāo)記器進(jìn)行時間和GPS同步。檢測球在管道內(nèi)運行時,電子系統(tǒng)記錄下管道上所有的特征信息(閥門、三通、彎頭、缺陷等)及其里程位置,結(jié)合放置在陰極保護(hù)測試樁處的地面標(biāo)記器所記錄的時間和GPS數(shù)據(jù),檢測結(jié)果可以得出缺陷異常點到最近陰極保護(hù)測試樁的相對距離,對缺陷異常點進(jìn)行準(zhǔn)確定位[3]。
里程輪法定位的管道距離信息可能會受管道內(nèi)污垢或滑動因素的影響,使測量數(shù)據(jù)產(chǎn)生誤差,因此,在開始漏磁內(nèi)檢測作業(yè)前,對該管道多次發(fā)射了機(jī)械清管球清理管壁結(jié)蠟和污垢。地面標(biāo)記系統(tǒng)測量需遵循地形,區(qū)段地形不一定與管道平行可能存在起伏,不能反映管道彎曲幾何形狀。采用地面標(biāo)記系統(tǒng)可以將檢測管道分段為1 km左右進(jìn)行位置標(biāo)記,以減少里程輪定位的累積誤差[4]。
4.3 開挖驗證過程
根據(jù)最終選取的8個缺陷異常點的詳細(xì)數(shù)據(jù),在管道沿線找到參考的陰極保護(hù)測試樁,以陰極保護(hù)測試樁為參考依據(jù),首先利用GPS定位儀測量缺陷異常數(shù)據(jù)表中給出的管道上下游環(huán)形焊縫位置,得到目標(biāo)缺陷異常點上下游環(huán)形焊縫的地表位置。然后根據(jù)缺陷異常點的環(huán)形焊縫與上下游螺旋焊縫交點的時鐘位置,判斷開挖的環(huán)形焊縫位置是否正確。
開挖過程中,由于管道上方涂層堅硬,先在土層表面開挖淺坑進(jìn)行注水,然后待土層濕潤后進(jìn)行人工開挖。開挖確定了環(huán)形焊縫位置,根據(jù)環(huán)形焊縫位置測量出缺陷點所在的環(huán)形軸距離,即可確定缺陷點的大體位置。開挖找到缺陷點大體位置,對缺陷點處的防腐蝕層進(jìn)行剝離,然后由檢測人員檢測驗證缺陷點位置,并測量缺陷點處的管壁剩余厚度。
4.4 開挖驗證結(jié)果
對內(nèi)檢測選取的8個缺陷異常點定位開挖,找到缺陷點明顯位置后,檢測人員綜合使用測厚儀、電火花檢漏儀和磁粉探傷儀等檢測設(shè)備,對開挖處的管道缺陷異常點進(jìn)行檢測和驗證。其中剩余厚度為漏磁內(nèi)檢測值,實測厚度為超聲波測厚儀實測值,相對誤差為漏磁內(nèi)檢測值與超聲波測厚儀實測值的相對誤差,具體的開挖驗證檢測數(shù)據(jù)和漏磁內(nèi)檢測數(shù)據(jù)對比信息見表9。
由表9可見:選取的8個漏磁內(nèi)檢測缺陷異常點中,除142.608 km處的缺陷點外,其他7個點的開挖驗證測量管壁剩余厚度與漏磁內(nèi)檢測設(shè)備檢測的相對誤差較小,為-5.31%~13.16%。
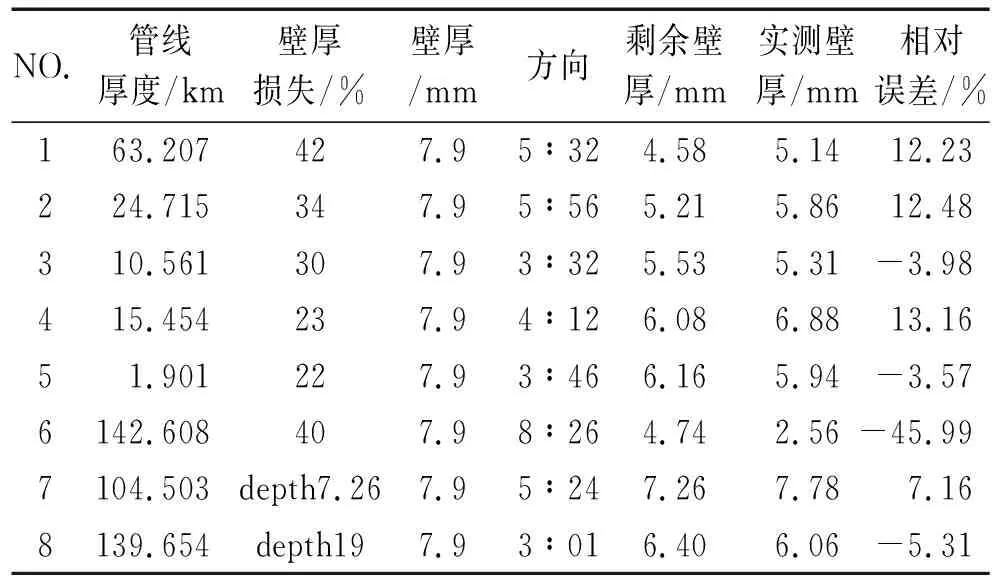
表9 8個實施開挖驗證異常點的管壁剩余厚度Tab. 9 Pipeline residual thickness measuring table of 8 anomalies performed excavation verification
對于壁厚損失為40%缺陷異常點,檢測公司在進(jìn)行漏磁內(nèi)檢測時,測量方向由管壁內(nèi)向管壁外,測量剩余壁厚為4.74 mm。而開挖驗證后使用測厚儀測量,測量方向由管壁外向管壁內(nèi),測量結(jié)果為2.56 mm,兩者偏差較大。此處管壁應(yīng)該存在出廠質(zhì)量問題,在管材鑄造的時候可能有氣泡混入,管壁存在中空區(qū)域。漏磁內(nèi)檢測設(shè)備的測量信號在遇到管壁中空區(qū)域即停止測量,所以管壁內(nèi)外測量顯示壁厚不同,且內(nèi)外單獨測量的管道壁厚均沒有反映此處的真實壁厚。
5 缺陷修復(fù)
對于開挖驗證后的8處內(nèi)檢測缺陷點,全部焊接B型套袖進(jìn)行修復(fù)。焊接采用合格堿性焊條,焊條加熱烘干320 ℃保溫0.5 h,母材預(yù)熱至100~120 ℃,焊接區(qū)域壁厚測量,焊接方法、焊接極性、焊接工藝都按照標(biāo)準(zhǔn)進(jìn)行。焊接作業(yè)中先焊接B型套袖兩條橫向焊縫,然后焊接下游側(cè)環(huán)形焊縫,最后焊接上游側(cè)環(huán)形焊縫。焊接完成后進(jìn)行焊縫外觀檢查,如果無明顯的咬邊,無夾渣,無氣孔,無熱裂紋,焊道寬度和高度均勻,外觀檢查合格。同時,對B型套袖兩條環(huán)形焊縫和兩條橫向焊縫做磁粉探傷檢測,檢測合格后方可視為B型套袖焊接合格。
B型套袖焊接完成后,對剝離防腐蝕層后裸露的金屬管道、B型套袖和焊縫周圍破損的防腐蝕層纏裹輻射交聯(lián)聚乙烯熱收縮纏繞帶。防腐蝕層修復(fù)完成后,再對開挖區(qū)域的管段防腐蝕層進(jìn)行電火花檢測,如果發(fā)現(xiàn)有防腐蝕層破損點,再用輻射交聯(lián)聚乙烯熱收縮纏繞帶進(jìn)行修復(fù),并重新進(jìn)行電火花檢測確認(rèn)無問題后,即可開展管道回填作業(yè)。在回填的過程中澆水,便于回填土下沉。
6 結(jié)論
針對原油管道漏磁內(nèi)檢測作業(yè)中檢測出的眾多異常點信息,主要依據(jù)國內(nèi)管道內(nèi)腐蝕評價標(biāo)準(zhǔn)規(guī)范對內(nèi)檢測結(jié)果中的9個最嚴(yán)重金屬損失點進(jìn)行了腐蝕評價和壓力分析,為需要維修的異常點選取提供了理論篩選依據(jù);同時介紹了8個漏磁內(nèi)檢測缺陷異常點進(jìn)行開挖驗證和缺陷修復(fù)的過程。通過分析漏磁內(nèi)檢測結(jié)果和開挖驗證結(jié)果,可以得到如下結(jié)論:
(1) 參考該原油管道異常點350萬t/a工況下的實際運行壓力和500萬t/a工況下的模擬運行壓力,應(yīng)該選9個最嚴(yán)重金屬損失點的最大安全工作壓力,作為該原油管道日常運行過程中各金屬損失點的壓力監(jiān)測值和控制上限值。
(2) 該原油管道漏磁內(nèi)檢測結(jié)果中篩選出的8個缺陷修復(fù)點,經(jīng)過開挖驗證工作后,除142.608 km處的缺陷點外,其他7個缺陷異常點的開挖驗證結(jié)果與漏磁內(nèi)檢測結(jié)果的剩余壁厚相對誤差較小,為-5.31%~10.04%。
(3) 對于存在中空區(qū)域的管壁,本次漏磁內(nèi)檢測過程中反滲透高分辨率機(jī)械檢測球測量的管壁剩余厚度和開挖驗證過程中測厚儀測量的管壁剩余厚度差值較大。漏磁內(nèi)檢測設(shè)備測量方向由管壁內(nèi)向管壁外,測厚儀測量方向由管壁外向管壁內(nèi),兩種測量設(shè)備發(fā)射的測量信號在遇到管壁中空區(qū)域都停止測量。所以兩種設(shè)備測量顯示的管壁厚度不同,且均沒有測量出此缺陷異常點處的真實管壁厚度。
(4) 在本次原油管道漏磁內(nèi)檢測作業(yè)中,除存在中空區(qū)域的管壁缺陷異常點外,該反滲透高分辨率機(jī)械檢測球?qū)υ凸艿拦鼙趦?nèi)側(cè)和外側(cè)缺陷異常點的測量置信水平和準(zhǔn)確程度都較高。