
由公式(9)易知初始變值側(cè)隙為,

因此,齒輪副總側(cè)隙及初始總側(cè)隙可表示為,

式中:jv、jv0、jφ、jφ0及jc分別為齒輪副變值側(cè)隙,初始變值側(cè)隙,總側(cè)隙,初始總側(cè)隙及常值側(cè)隙,單位均為度(°).
1.3 雙齒面無負(fù)載傳動誤差與側(cè)隙關(guān)系
通過前文計算公式可知,

由上式可知,齒輪副側(cè)隙可間接通過驅(qū)動齒面無負(fù)載傳動誤差及含初始側(cè)隙的齒背面無負(fù)載傳動誤差得到.
2 雙齒面?zhèn)鲃诱`差測量
2.1 實(shí)驗(yàn)裝置及參數(shù)
實(shí)驗(yàn)裝置如圖3,實(shí)驗(yàn)系統(tǒng)包括驅(qū)動電機(jī)、變齒厚齒輪副、編碼器、負(fù)載電機(jī)、滾珠花鍵副、數(shù)據(jù)采集系統(tǒng)、電機(jī)的控制器、直線執(zhí)行器、消隙控制器以及上位機(jī)等. 通過控制器1控制驅(qū)動電機(jī)旋轉(zhuǎn),控制器2控制負(fù)載電機(jī)提供實(shí)驗(yàn)所需負(fù)載,主從動輪轉(zhuǎn)動角度分別通過編碼器1和2測量,測量的角位移數(shù)據(jù)由數(shù)據(jù)采集系統(tǒng)采集并帶入公式(14)計算,從而獲得雙齒面實(shí)驗(yàn)傳動誤差曲線. 由于本實(shí)驗(yàn)僅涉及傳動誤差及側(cè)隙測量,并未涉及消隙實(shí)驗(yàn),因此消隙控制器及直線執(zhí)行器未使用,但連續(xù)側(cè)隙的測試對消隙控制研究具有重要意義[22?24].此外,本裝置中的變齒厚齒輪副屬于漸開線齒輪副一種,因此上述建立的傳動誤差及側(cè)隙理論模型仍然適用. 實(shí)驗(yàn)參數(shù)及齒輪副參數(shù)如表1.

式中,? ?為傳動誤差,φ2s分別為編碼器2測量角位移,φ1s為 編碼器1測量角位移,i為傳動比.
2.2 雙齒面?zhèn)鲃诱`差測量
當(dāng)驅(qū)動電機(jī)驅(qū)動主動齒輪旋轉(zhuǎn),其方向與負(fù)載力矩方向均為逆時針時,若啟動時開始接觸齒面為驅(qū)動齒面,如圖4(a),實(shí)驗(yàn)所測的傳動誤差曲線為初始無側(cè)隙驅(qū)動齒面?zhèn)鲃诱`差;若啟動時開始接觸齒面為齒背面,如圖4(b),則實(shí)驗(yàn)所測的傳動誤差曲線為含初始側(cè)隙的驅(qū)動齒面?zhèn)鲃诱`差.當(dāng)驅(qū)動電機(jī)驅(qū)動主動齒輪逆時針旋轉(zhuǎn),負(fù)載力矩方向?yàn)轫槙r針方向時,若啟動時開始接觸齒面為驅(qū)動齒面,如圖5(a),實(shí)驗(yàn)所測的傳動誤差曲線為含初始側(cè)隙的齒背面?zhèn)鲃诱`差;若啟動時開始接觸齒面為齒背面,如圖5(b),則實(shí)驗(yàn)所測的傳動誤差曲線為初始無側(cè)隙齒背面?zhèn)鲃诱`差. 由于主從動輪齒數(shù)的關(guān)系,當(dāng)主動輪旋轉(zhuǎn)16圈,從動輪旋轉(zhuǎn)9圈時,齒輪嚙合的輪齒相同,齒輪副回到初始測試起點(diǎn). 為方便進(jìn)行實(shí)驗(yàn)結(jié)果比較,主動輪每次均由相同起始位置開始,起始位置的精度由編碼器保證. 實(shí)驗(yàn)中為保證實(shí)驗(yàn)數(shù)據(jù)的可靠性,每組數(shù)據(jù)均進(jìn)行重復(fù)性實(shí)驗(yàn).
2.3 傳動誤差實(shí)驗(yàn)曲線與初步分析
按圖4~圖5所示初始位置,分別進(jìn)行不同負(fù)載力矩下的雙齒面?zhèn)鲃诱`差曲線測量,實(shí)驗(yàn)結(jié)果如圖6~圖9. 定義回差為負(fù)載下實(shí)驗(yàn)裝置的變形與齒輪副側(cè)隙值之和,即

式中,B為回差,? δk為負(fù)載引起的變形.
因此,初始時刻的回差(以下簡稱初始回差)為負(fù)載引起的變形和齒輪副初始側(cè)隙之和,即

式中,B0為初始回差
由實(shí)驗(yàn)裝置圖3可知,負(fù)載引起的變形和齒輪副初始側(cè)隙為編碼器2在初始時刻測量所得角度值的絕對值,而初始時刻編碼器1測量角度值因此,

式中,B0為初始回差,? ?0為傳動誤差初始值.
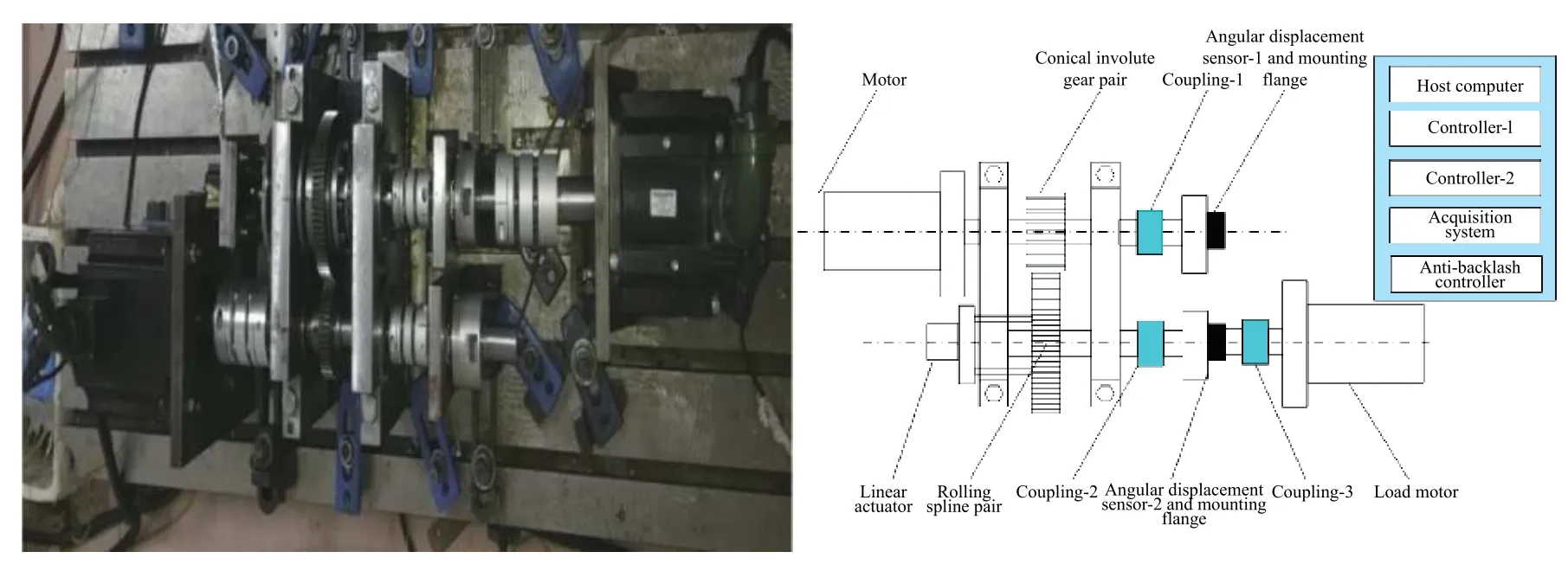
圖3 傳動誤差及側(cè)隙測量實(shí)驗(yàn)裝置圖Fig.3 Experimental device for transmission error and backlash measurement
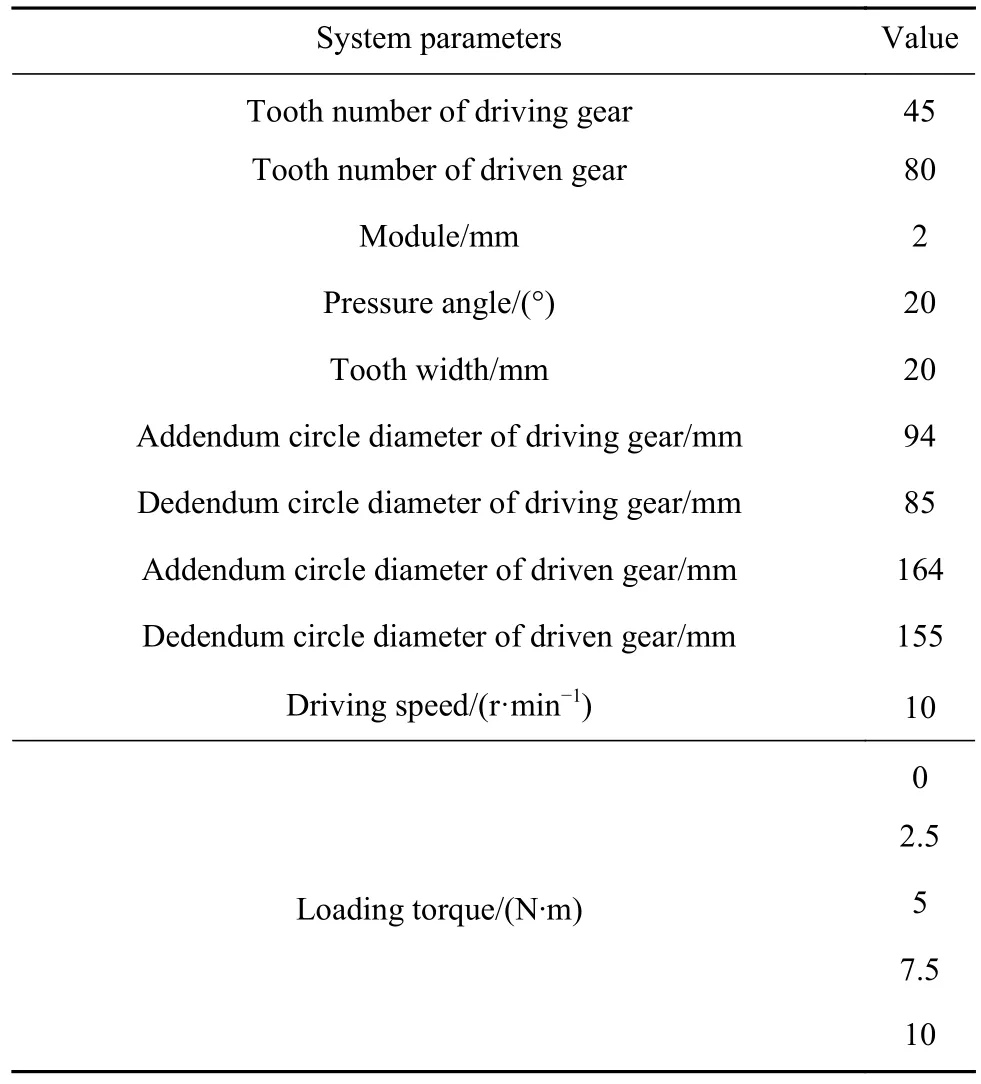
表1 齒輪副基本參數(shù)Table 1 Basic parameters of gear pair
由公式(17)知,初始回差即為初始時刻傳動誤差值絕對值. 圖6(a)中為不同負(fù)載的驅(qū)動齒面?zhèn)鲃诱`差曲線,同時由于初始接觸齒面為驅(qū)動齒面,即齒輪副初始側(cè)隙為零,聯(lián)立公式(16)及(17)可知,傳動誤差曲線的初始時刻值的絕對值(即初始回差)等于負(fù)載引起的變形值. 當(dāng)負(fù)載力矩為零時,負(fù)載引起的變形為零,因此傳動誤差曲線初始時刻值為零. 而隨著負(fù)載力矩逐漸增加,導(dǎo)致齒輪、軸、聯(lián)軸器等零件變形加大,初始回差逐漸增大,因此傳動誤差曲線初始時刻值的絕對值逐漸增大,即逐漸遠(yuǎn)離坐標(biāo)原點(diǎn). 由各負(fù)載下傳動誤差初始時刻值及公式(17)可得相應(yīng)負(fù)載下的初始回差實(shí)驗(yàn)值,如圖6(b)所示,而初始回差理論值由計算所得,將在 2.4節(jié)具體闡述. 此外,從圖 6(b)可知,負(fù)載力矩與初始回差呈較好的線性關(guān)系.
圖7(a)所示,由于初始接觸齒面發(fā)生變化,齒輪副初始側(cè)隙值不為零,因此,傳動誤差曲線初始時刻為初始側(cè)隙值與負(fù)載引起的變形值之和. 當(dāng)負(fù)載為零時,負(fù)載引起的變形為零,因此由公式(16)及公式(17)可知,傳動誤差初始時刻值的絕對值即為齒輪副初始側(cè)隙,即約為0.065°. 同時由各負(fù)載下傳動誤差初始時刻值及公式(17)可得相應(yīng)負(fù)載下的初始回差實(shí)驗(yàn)值,如圖 7(b)所示. 圖 7(b)中,初始回差與負(fù)載也呈較好的線性關(guān)系.
同理可分析圖8與圖9齒背面?zhèn)鲃诱`差曲線與初始回差. 圖8(a)中,當(dāng)初始時刻接觸面為驅(qū)動齒面時,齒輪副初始側(cè)隙不為零,初始回差為齒輪副初始側(cè)隙及實(shí)驗(yàn)裝置變形之和;圖9(a)中,當(dāng)初始時刻接觸面為齒背面時,齒輪副初始側(cè)隙為零,因此初始回差等于實(shí)驗(yàn)裝置變形. 此外,如圖8(b)與9(b)所示,初始回差與負(fù)載也呈較好的線性關(guān)系,且變化斜率基本與圖 6(b)、圖 7(b)一致.

圖4 驅(qū)動齒面?zhèn)鲃诱`差測量起始位置示意圖. (a)初始接觸齒面為驅(qū)動齒面;(b)初始接觸齒面為齒背面Fig.4 Schematic of the initial position of the drive-side transmission error measurement:(a) drive-side contact in initial position; (b) back-side contact in initial position
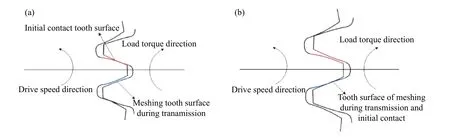
圖5 齒背面?zhèn)鲃诱`差測量起始位置示意圖. (a)初始接觸齒面為驅(qū)動齒面;(b)初始接觸齒面為齒背面Fig.5 Schematic of the initial position of the back-side transmission error measurement:(a) drive-side contact in initial position; (b) back-side contact in initial position
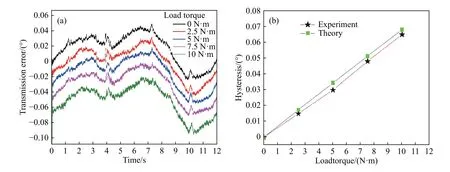
圖6 驅(qū)動齒面?zhèn)鲃诱`差測量且初始時刻驅(qū)動齒面接觸. (a)傳動誤差對比曲線;(b)各負(fù)載與其初始回差對比Fig.6 Drive-side transmission error measurement with drive-side contact at initial position:(a) comparison of transmission error curves; (b) comparison of each load torque with its corresponding hysteresis

圖7 驅(qū)動齒面?zhèn)鲃诱`差測量且初始時刻齒背面接觸. (a)傳動誤差對比曲線;(b)各負(fù)載與其初始回差對比Fig.7 Drive-side transmission error measurement with back-side contact at initial position:(a) comparison of transmission error curves; (b) comparison of each load torque with its corresponding hysteresis

圖8 齒背面?zhèn)鲃诱`差測量且初始時刻驅(qū)動齒面接觸. (a)傳動誤差對比曲線;(b)各負(fù)載與其初始回差對比Fig.8 Back-side transmission error measurement with drive-side contact at initial position:(a) comparison of transmission error curves; (b) comparison of each load torque with its corresponding hysteresis
2.4 剛度計算與初始回差分析
從圖3實(shí)驗(yàn)裝置圖可知,當(dāng)施加負(fù)載力矩時,編碼器2測量的角度中包含的變形主要是齒輪副變形、滾珠花鍵副變形、膜片聯(lián)軸器2變形及從動輪至編碼器2之間的輸出軸變形. 因此總變形可以表示下,

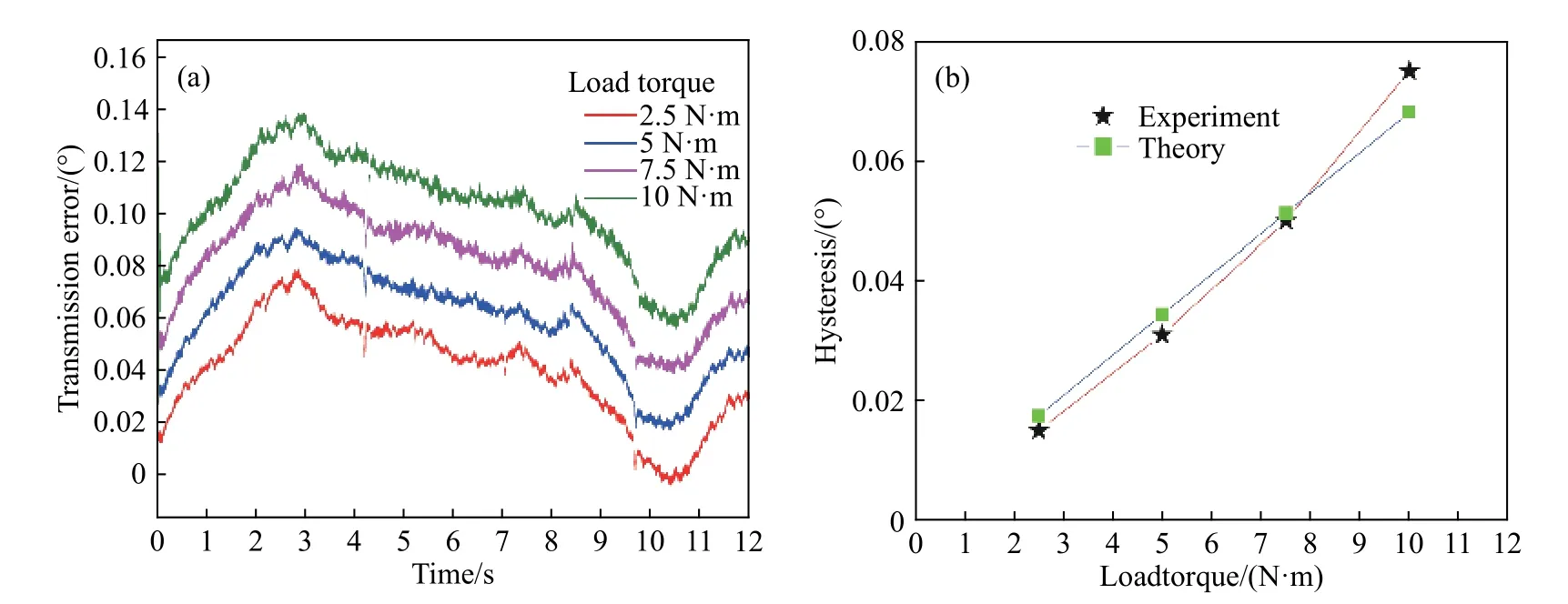
圖9 齒背面?zhèn)鲃诱`差測量且初始時刻齒背面接觸. (a)傳動誤差對比曲線;(b)各負(fù)載與其初始回差對比Fig.9 Back-side transmission error measurement with back-side contact at initial position:(a) comparison of transmission error curves; (b) comparison of each load torque with its corresponding hysteresis.
式中,T為負(fù)載力矩,kg、ka、ks及kc分別為單位寬度齒輪副剛度、從動輪至編碼器2之間的輸出軸剛度、滾珠花鍵副剛度及聯(lián)軸器剛度. 其中,單位寬度齒輪副剛度通過文獻(xiàn) [20]查得為 20 N?(μm·mm)?1,軸的剛度由文獻(xiàn) [25]得 289.44 N?m?(°)?1,滾珠花鍵副剛度參考文獻(xiàn) [26]計算后為 9.768×107?P1/3N?m?1,其中P為外載作用力,膜片聯(lián)軸器剛度參考文獻(xiàn)[25]為 1.87×104N?m?rad?1. 各部分剛度及變形如表 2、表3所示.
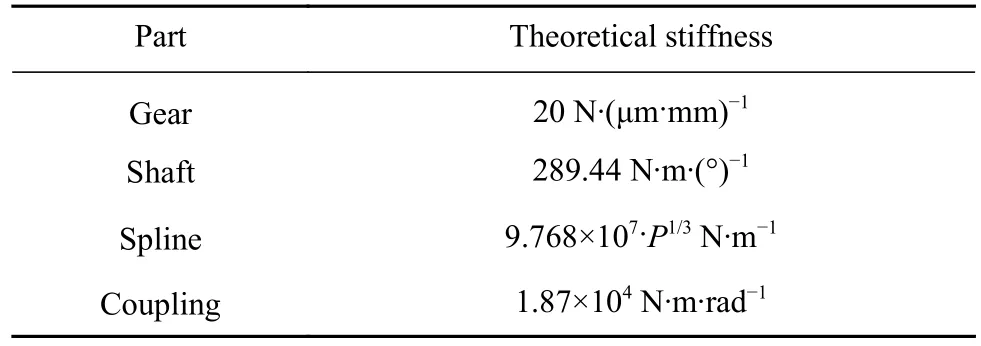
表2 各部分理論剛度Table 2 Theoretical stiffness of each part

表3 不同負(fù)載力矩下,各部分變形數(shù)據(jù)Table 3 Deformation data of various parts under different loads
從表3可以看出,各負(fù)載力矩下實(shí)驗(yàn)總變形結(jié)果與理論結(jié)果吻合較好,且引起變形回差的主要因素是軸和聯(lián)軸器. 由公式(16)可知,初始回差主要由實(shí)驗(yàn)裝置變形和齒輪副初始側(cè)隙組成,因此變形越大,初始回差越大. 同時表2中,軸與聯(lián)軸器剛度相對較低,即變形較大,因此對初始回差影響較大.
聯(lián)立公式(16)及(18)得

由公式(19)可知,初始回差與負(fù)載之間理論上呈線性關(guān)系. 將表3中各負(fù)載下計算的理論變形值以及2.3節(jié)的齒輪副初始側(cè)隙值代入公式(16),得到理論初始回差,如圖 6(b)、圖 7(b)、圖 8(b)及圖 9(b). 由圖 6(b)~圖 9(b)可知,實(shí)驗(yàn)和理論初始回差吻合較好,且均與負(fù)載具有較好的線性關(guān)系.
3 側(cè)隙連續(xù)曲線與預(yù)測
3.1 側(cè)隙連續(xù)曲線
當(dāng)通過公式(13)獲得齒輪副連續(xù)側(cè)隙曲線時,雙齒面?zhèn)鲃诱`差曲線必須為無負(fù)載傳動誤差曲線. 由圖 6(a)~圖 9(a)可知,負(fù)載下的傳動誤差曲線與無負(fù)載下的傳動誤差曲線為常值的上下偏移,其偏移值與表3中計算的變形值相等,即

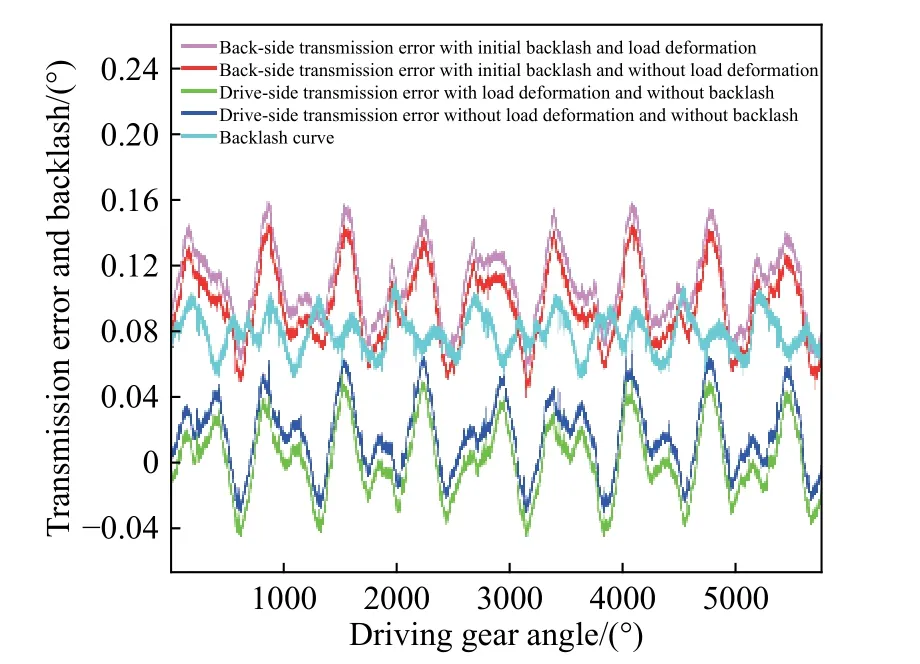
圖10 雙面?zhèn)鲃诱`差與側(cè)隙連續(xù)曲線Fig.10 Two-sided transmission error and continuous backlash curve
3.2 側(cè)隙預(yù)測
3.2.1 初始側(cè)隙、偏心誤差及其初始相位預(yù)測
不同于上述側(cè)隙連續(xù)測量方法,側(cè)隙預(yù)測只需采集一段含初始側(cè)隙的齒背面?zhèn)鲃诱`差曲線,以2.5 N?m含初始側(cè)隙的驅(qū)動面?zhèn)鲃诱`差實(shí)驗(yàn)曲線為例,如圖11,易知初始回差為0.08°,除去負(fù)載力矩引起的理論變形量0.015°(第2部分剛度計算中已求),因此齒輪副初始側(cè)隙jφ0為0.065°. 再將不含初始回差的齒背面?zhèn)鲃诱`差曲線帶入其理論模型公式(6),通過實(shí)驗(yàn)數(shù)據(jù)擬合,從而預(yù)測出齒輪副的偏心誤差及其初始相位,擬合曲線如圖11,擬合得到偏心誤差和初始相位分別為:e1=0.023 mm,θ1= ?12.9?,e2=0.026 mm,θ2= ?69.8?.
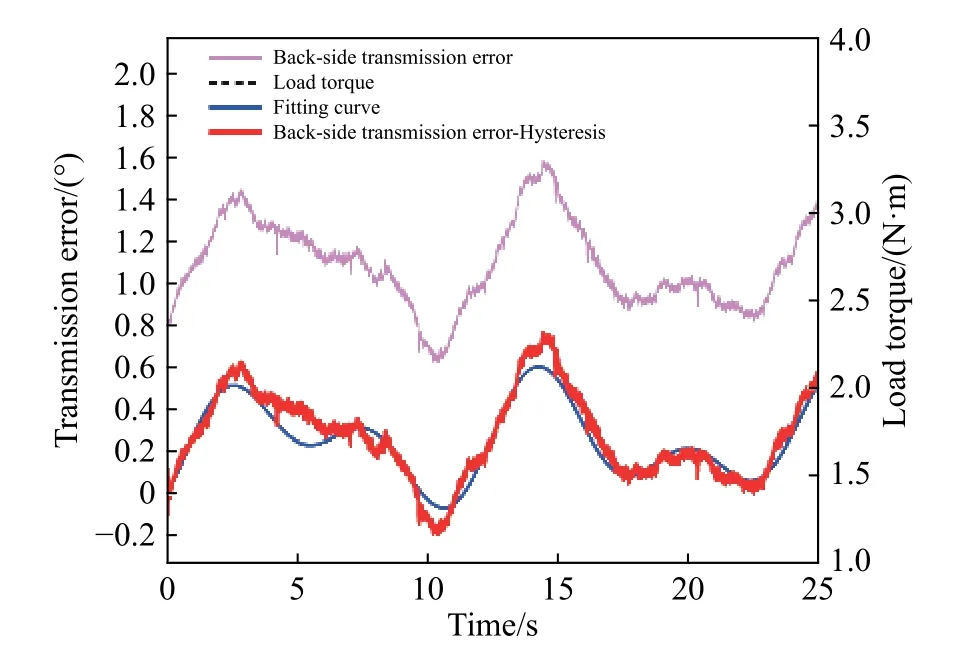
圖11 齒背面?zhèn)鲃诱`差實(shí)驗(yàn)及擬合曲線Fig.11 Experimental and fitting curve of back-side transmission error
3.2.2 變值側(cè)隙、常值側(cè)隙及總側(cè)隙預(yù)測
將擬合得到的偏心誤差及初始相位帶入側(cè)隙模型公式(9)得到變值側(cè)隙,如圖12. 再通過公式(10),得初始變值側(cè)隙jv0為?0.007°,并由初始側(cè)隙和初始變值側(cè)隙值,通過公式(12)得常值側(cè)隙為0.072°,最后得到齒輪副總側(cè)隙,如圖12所示.

圖12 側(cè)隙預(yù)測曲線Fig.12 Predicted backlash curve
4 側(cè)隙測量方法對比
如圖13所示,機(jī)械滯后回差測量法是將主動輪固定,再將從動輪分別轉(zhuǎn)動到驅(qū)動齒面接觸和齒背面接觸兩個位置,記錄兩個位置的角度值并相減,并除去該力矩下引起的變形角度,從而得到該位置處齒輪副的側(cè)隙值. 再將主動轉(zhuǎn)動一定角度,重復(fù)上面操作,從而得到一組離散的側(cè)隙值曲線. 本實(shí)驗(yàn)在一個大周期內(nèi)(主動輪16圈,從動輪9圈)以及 2.5 N?m 負(fù)載力矩下,主動輪從 0°到 5760°每旋轉(zhuǎn)90°測試一組側(cè)隙值,共計65組側(cè)隙數(shù)據(jù),測量結(jié)果如圖14.

圖13 機(jī)械滯后回差法測量原理Fig.13 Measurement principle of mechanical return backlash method
圖14為三種側(cè)隙測量方法測試結(jié)果,可以看出側(cè)隙連續(xù)測量與機(jī)械滯后回差法測量的結(jié)果十分吻合,證明了基于雙齒面?zhèn)鲃诱`差的側(cè)隙測量方法的正確性. 三種方法中,機(jī)械滯后回差法數(shù)據(jù)零散且不全面,且耗費(fèi)時間周期長,效率低;基于雙齒面?zhèn)鲃诱`差的側(cè)隙連續(xù)測量方法不需要單點(diǎn)進(jìn)行測量,可以獲得更全面的側(cè)隙數(shù)據(jù),且整個大周期側(cè)隙結(jié)果僅在幾分鐘內(nèi)便可全部得到,效率較高;側(cè)隙預(yù)測方法效率最高,僅需測量一小段含側(cè)隙的齒背面?zhèn)鲃诱`差而得到整個大周期側(cè)隙結(jié)果,但與其余兩種方法相比,其結(jié)果存在有一定偏差,因?yàn)閿M合得到的偏心誤差與其初始相位以及計算的理論剛度值均與實(shí)際情況存在偏差,因此此方法只能大致預(yù)測側(cè)隙值范圍以及側(cè)隙在整個大周期內(nèi)的變化趨勢.
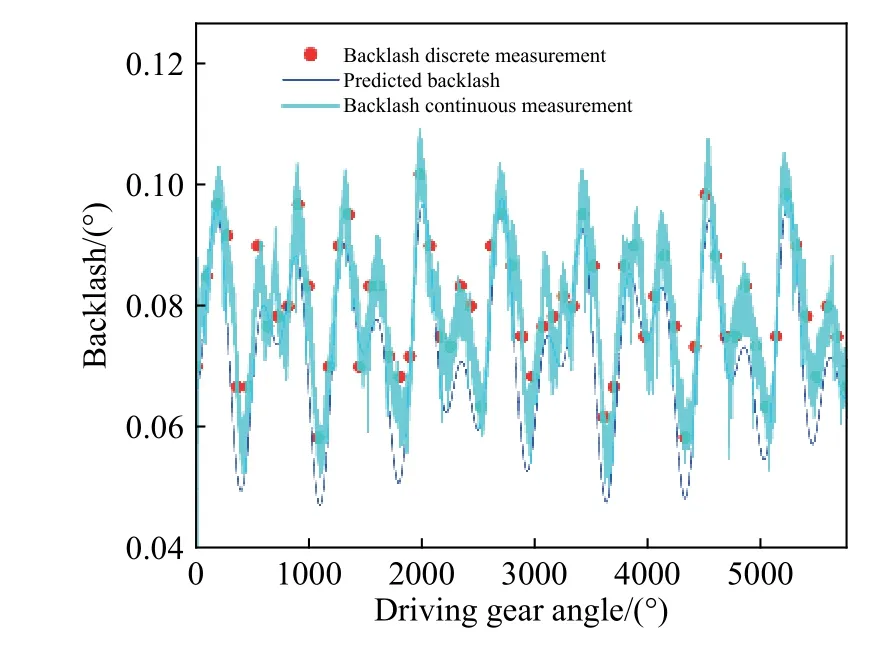
圖14 三種側(cè)隙測量方法對比Fig.14 Comparison of three backlash measurement methods
5 結(jié)論
(1)本文建立雙齒面?zhèn)鲃诱`差及側(cè)隙理論模型并建立三者等價關(guān)系. 進(jìn)行了不同負(fù)載力矩下雙齒面?zhèn)鲃诱`差的測量. 結(jié)果表明負(fù)載力矩與初始回差呈較好的線性關(guān)系,負(fù)載力矩越大,變形越大,初始回差越大. 經(jīng)過剛度理論計算發(fā)現(xiàn)引起變形回差的主要部分為膜片聯(lián)軸器與輸出軸,齒輪和滾珠花鍵影響較小.
(2)基于雙齒面?zhèn)鲃诱`差實(shí)驗(yàn)曲線,實(shí)現(xiàn)了對齒輪整個大周期側(cè)隙的連續(xù)測量與預(yù)測. 結(jié)果表明,連續(xù)測量曲線與機(jī)械滯后回差法測量結(jié)果吻合良好,而側(cè)隙預(yù)測較好地反應(yīng)了側(cè)隙值變化范圍和變化趨勢. 同時,測量連續(xù)測量方法及側(cè)隙預(yù)測均證明了理論模型的正確性,提高了側(cè)隙測量效率并獲得了更全面的側(cè)隙數(shù)據(jù),為齒輪傳動的非線性研究、消隙控制以及齒輪精度研究等奠定了基礎(chǔ).